Forschungsprojekt zu Metall-Polymer-Stromkollektoren zur Steigerung der Sicherheit von Lithium-Ionen-Batterien
Im August 2021 startete das vom Bundesministerium für Bildung und Forschung (BMBF) geförderte Projekt PolySafe (Förderkennzeichen 03XP0408). Ziel von PolySafe ist es, die Sicherheit von Lithium-Ionen-Batterien durch den Einsatz neuartiger Stromkollektoren zu steigern. Im Fokus stehen dabei Metall-Polymer-Komposit-Stromkollektoren, die das thermische Durchgehen von Batteriezellen verhindern und damit die Brandgefahr verringern. An dem mit knapp 4 Millionen Euro geförderten Projekt sind die VON ARDENNE GmbH, die Brückner Maschinenbau GmbH & Co. KG, das Fraunhofer-Institut für Organische Elektronik, Elektronenstrahl- und Plasmatechnik FEP, das Fraunhofer-Institut für Schicht- und Oberflächentechnik IST, die Battery LabFactory Braunschweig der TU Braunschweig sowie die Varta Microbattery GmbH beteiligt.
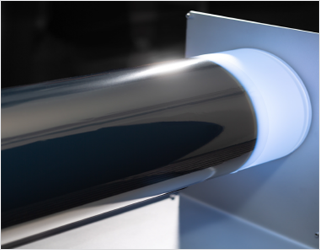
Die Machbarkeit der Herstellung der Metall-Polymer-Stromkollektoren wurde bereits gemeinsam von der VON ARDENNE GmbH und dem Fraunhofer FEP im Rahmen des sächsischen Forschungsvorhabens PolyCollect demonstriert. Durch das Verfahren der physikalischen Gasphasenabscheidung konnten bis zu 1 µm dicke Aluminiumschichten auf Polymersubstraten mit Dicken bis 8 µm erzeugt werden. Allerdings existieren bisher zu wenige Daten aus Prototypzellen mit diesem Material, weshalb die anwendungsnahe Evaluation dieser Technologie noch aussteht. Das soll nun im Rahmen von PolySafe geschehen. Das Ziel ist, eine an die Metall-Polymer-Stromkollektoren angepasste Prozesskette zur Herstellung von Batteriezellen in verschiedenen Formaten (Rundzelle, Pouchzelle) zu qualifizieren und den Sicherheitsvorteil in unterschiedlichen Zelldesigns- und -chemien anwendungsnah zu untersuchen.
Neben der Integration der hergestellten Metall-Polymer-Stromkollektoren in Batteriezellen wollen die Projektpartner Aluminium- bzw. Kupfer-Polymer-Stromkollektoren dediziert an die Anforderungen des jeweiligen Zelldesigns anpassen und optimieren. Die Herausforderung ist, die Polymersubstrate und den Beschichtungsprozess so auszulegen, dass eine zu aktuellen Metallfolien vergleichbare Dicke sowie eine optimale elektrische Leitfähigkeit der Metallschicht gewährleistet ist. Zugleich verfolgen die Partner das Ziel, die Produktionskosten der Stromkollektoren auf ein konkurrenzfähiges Niveau zu bringen.
Die VON ARDENNE GmbH übernimmt die Koordination des Forschungsprojektes PolySafe. Außerdem wird das Dresdner Unternehmen – ausgehend von den Ergebnissen der technologischen Entwicklung beim Fraunhofer FEP – sein Know-how zur technischen Konzeption einer Produktionsanlage zur Abscheidung der Metallschichten einbringen, die sowohl die technologischen als auch die wirtschaftlichen Anforderungen an eine Produktion von Metall-Polymer-Stromkollektoren erfüllt.
Die Brückner Maschinenbau GmbH & Co.KG arbeitet an der Entwicklung von Polymerfolien, die sowohl an die Anforderungen der Metallisierung als auch der Anwendung in Batterien angepasst sind. Dabei gilt es, innovative Polymersubstrate und Oberflächenbehandlungen zu entwickeln und zum Rollenmaßstab zu skalieren. Die vielversprechendsten Materialien sollen als Substrate zur Metallisierung zur Verfügung gestellt werden.
Die Wissenschaftler des Fraunhofer FEP entwickeln eine geeignete technologische Prozessführung zur Abscheidung der Aluminium- und Kupferschichten in einem Rolle-zu-Rolle-Prozess. Es gilt dabei, den Einfluss von Parametern des Bandlaufs, der Substratvorbehandlung sowie der Metallverdampfung ganzheitlich zu verstehen und optimale Prozesseinstellungen zur Erreichung der technologischen und wirtschaftlichen Anforderungen zu entwickeln.
Die Battery LabFactory Braunschweig der Technischen Universität Braunschweig bringt ihre Kompetenzen zum Produktionsprozess und zur Charakterisierung von Elektroden und Pouchzellen für Lithium-Ionen-Batterien ein. Die Metall-Polymer-Stromkollektoren werden hinsichtlich ihrer Eignung zur Integration in die Produktionsprozesse von Lithium-Ionen-Batterien untersucht und – wenn notwendig – die Fertigungsverfahren gezielt angepasst.
Das Fraunhofer IST erforscht die Eignung der Metall-Polymer-Stromkollektoren für neuartige Batteriezellgenerationen, insbesondere mit dem Fokus auf die Lithium-Metall-Anoden. Ein besonderer Schwerpunkt wird dabei auf den Fertigungsschritten der Lithium-Metall-Anoden und der resultierenden Zellen liegen.
VARTA Microbatteries übernimmt die Integration der neuen Elektroden mit Metall-Polymerstromkollektoren in Vollzellen und die normgerechte Sicherheitstestung. Insbesondere soll dabei die Prozessierung und Sicherheit von Rundzellen mit Metall-Polymerstromkollektoren untersucht und mit reinen Metallfolien verglichen werden.
ÜBER DIE VON ARDENNE-GRUPPE
VON ARDENNE entwickelt und fertigt Anlagen für die industrielle Vakuumbeschichtung von Materialien wie Glas, Wafer, Metallband oder Kunststofffolie. Je nach Anwendung sind diese Schichten einen Nanometer bis wenige Mikrometer dünn und verleihen den Oberflächen neue funktionale Eigenschaften. Die beschichteten Materialien sind die Basis für Produkte wie Architekturglas, Solarmodule, Touch-Screens, Lithium-Ionen-Batterien, Brennstoffzellen oder Präzisionsoptiken.
VON ARDENNE ist ein führender Anbieter von Architekturglas-Beschichtungsanlagen und Beschichtungssystemen für die Dünnschicht-Photovoltaik. Das Familienunternehmen beschäftigt weltweit rund 1000 Mitarbeiter und hat seinen Sitz in Dresden. Als global tätiges Unternehmen mit Niederlassungen in China, Japan, Malaysia, Vietnam und den USA setzt VON ARDENNE auf Kundennähe, um idealen Vor-Ort-Service zu bieten. VON ARDENNE-Anlagen sind in mehr als 50 Ländern im Einsatz.
ÜBER DIE BRÜCKNER MASCHINENBAU GMBH & CO.KG
Brückner Maschinenbau ist eines der weltweit führenden Unternehmen im Anlagenbau für die Herstellung von monoaxial und biaxial verstreckten Kunststofffolien. Durch die Fähigkeit, Prozess und Material gemeinsam zu betrachten, ist Brückner Maschinenbau in der Lage, auch für Zukunftstechnologien im Batteriebereich neue Maßstäbe zu setzen. So kann PET-Folie mit Dicken < 1 μm im Produktionsmaßstab hergestellt werden. Durch ein umfassend ausgestattetes Technikum können die für das skizzierte Projekt zu untersuchenden Zusammenhänge zwischen Rohstoff, Prozess und Endprodukt adressiert werden.
ÜBER DAS FRAUNHOFER-INSTITUT FÜR ORGANISCHE ELEKTRONIK, ELEKTRONENSTRAHL- UND PLASMATECHNIK FEP
Das Fraunhofer FEP verfügt über umfangreiche Erfahrungen im Bereich der Technologieentwicklung zur Abscheidung dünner Schichten auf großen Flächen in RzR-Verfahren mit hoher Produktivität. Die Entwicklungsergebnisse wurden bereits mehrfach in industrielle Lösungen umgesetzt. Innerhalb einiger Forschungsprojekte mit Partnern aus der Industrie und Forschung sind im FEP entwickelte Dünnschicht-technologien für die Batterietechnik untersucht und zum Teil sogar bis zur Pilotreife geführt wurden.
ÜBER DAS FRAUNHOFER-INSTITUT FÜR SCHICHT- UND OBERFLÄCHENTECHNIK IST
Das Fraunhofer-Institut für Schicht- und Oberflächentechnik IST forscht und entwickelt in den Bereichen Materialsynthese und -funktionalisierung, Oberflächenbehandlung und -modifikation, Schichtherstellung und -anwendung, Schichtcharakterisierung und Oberflächenanalyse sowie im Bereich der Produktionstechnik. Die Batterieforschung als zentrales Thema der Abteilung „Verfahrens- und Fertigungstechnik für nachhaltige Energiespeicher“ des Fraunhofer IST beschäftigt sich mit der Material- und Energiespeicherentwicklung, inkl. zugehöriger Verfahrens- und Fertigungstechniken. Das Institut betreibt seit 2019 in Braunschweig gemeinsam mit dem Fraunhofer IKTS und dem Fraunhofer IFAM das Fraunhofer- Projektzentrum für Energiespeicher und Systeme ZESS, welches die Produktion innovativer mobiler und stationäre Energiespeicher skaliert und an die industrielle Reife heranführt.
ÜBER TU BRAUNSCHWEIG, BATTERY LABFACTORY BRAUNSCHWEIG
Die Battery LabFactory Braunschweig (BLB) der TU Braunschweig vernetzt als transdisziplinäres Zentrum 14 Institute zur ganzheitlichen Forschung und Entwicklung von batterieelektrischen Speichertechnologien und erstreckt sich über den gesamten Wertschöpfungskreislauf von der Materialherstellung über die Zellfertigung bis zum Recycling zur Schließung des Materialkreislaufes. In einer „Joint Pilot Facility“ wird die Elektroden- und Zellfertigung sowie die Zellkonditionierung in technischen, automatisierten Prozessen im Technikums- bis Pilotmaßstab abgebildet (Batterie-Technologieplattform 1000 m2 davon 200 m2 Trockenraum, zudem 700 m2 Technika für Analytik und Post-Mortem- Analyse), so dass definiert gefertigte Zellen im Großformat für Batterie-Demonstratoren abgebildet werden können. Speziell im Projekt eingebracht wird i) die seit 2007 etablierte Prozess- und Produktkompetenz in der Elektrodenfertigung, ii) die Kompetenz in Produktions-, Fertigungs-, Füge- und Handhabungstechnologie im Bereich der Zellassemblierung, Konfektionierung, Kontaktierung iii) Methodenkompetenz für die energieorientierte Modellbildung und die Ökobilanzierung, sowie iv) elaborierte Prozeduren für Formierung und Zyklisierung zur Zellkonditionierung sowie Diagnosemethoden.
ÜBER DIE VARTA MICROBATTERY GMBH
Bei VARTA Microbattery GmbH (VMB) wurde seit 1998 an Lithium-Ionen-Zellen geforscht. Das bei VMB vorhandene Fachwissen, speziell im Bereich der Produktionstechnik, wurde für den erfolgreichen Aufbau einer Fertigung für Lithium-Ionen Kleinstzellen (CoinPower®) stetig weiterentwickelt. Daneben wurde das aus dem Joint-Venture „Volkswagen VARTA Microbattery Forschungsgesellschaft mbH & Co. KG“ (VWVM, 2010- 2017) gewonnene Fachwissen zur weiteren Erforschung, sowie dem Aufbau einer Pilotlinie von 21700-Rundzellen verwendet. Beide Technologien sollen im Rahmen von PolySafe genutzt werden. Durch die langjährige Erfahrung mit elektrochemischen Energiespeichern, zum Beispiel auch aus den Projekten EffiForm, Oekobat-2020 oder RONDO ist VMB für die im Projekt PolySafe geplanten Arbeiten hervorragend geeignet.
PolySafe
Forschungsprojekt zur Steigerung der Sicherheit von Lithium-Ionen-Batterien durch Metall-Polymer-Komposit-Stromkollektoren
Förderkennzeichen: 03XP0408